Hon Hai Precision - Truthss
Wiki Article
About Manufacturing Industries
Table of Contents4 Simple Techniques For Lean ManufacturingRumored Buzz on Manufacturing IndustriesMfg Can Be Fun For AnyoneThe Facts About Manufacturing Industries UncoveredA Biased View of ManufacturingFascination About Oem
The text on this page is an example from our complete White Paper 'Injection Moulding for Buyers' - * Sample message * - for complete guide click the download switch over! Introduction This overview is intended for individuals who are aiming to resource plastic mouldings. It provides a much needed insight into all that is entailed with creating plastic components, from the mould device needed to the moulding process itself.If you intend to discover better, the overview covers sorts of mould tools, as well as unique ending up processes such as colours & plating. Words that are underlined can be located in the reference in the appendix ... Component I: Moulding: The Fundamentals The Advantages of Shot Moulding Plastic injection moulding is a very specific process that uses a number of advantages over other plastic processing approaches.
Accuracy is excellent for extremely detailed components. Contrasted to various other techniques, moulding enables you to incorporate even more attributes at extremely tiny resistances. Have a look at the photo to the. You can hold this moulding in the palm of your hand and it has employers, ribs, metal inserts, side cores and openings, made with a gliding shut down attribute in the mould tool.
The Facts About Die Casting Uncovered
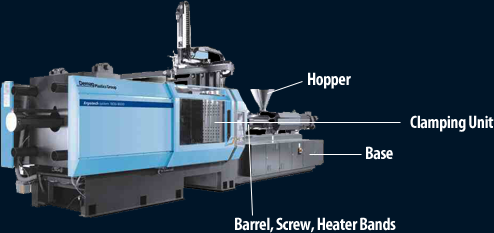

from product feed & melting; material shot; cooling time and also ejection to the re-closing of the mould device prepared for the following cycle. Draft angles - The walls of a moulded part must be slightly tapered in the instructions in which the part is ejected from the mould tool, to permit the part to be expelled quickly.
Ejector stroke - The pushing out of ejector pins to eject the moulded part from the mould device. Ejector stroke speed, length and timing requires to be very carefully managed to avoid damage to the ejectors and also mould tool, but at the very discover this same time make the moulding cycle as short as feasible.

How Plastic Manufacturing can Save You Time, Stress, and Money.
Ribs - When a plastic part has slim walls, ribs are added to the style to make the thin walls more powerful Side cores - Side activity which creates an attribute on a moulded component, at an opposing angle to the normal opening direction of the mould device. die casting. The side core requires to be able to withdraw as the plastic component can not be expelled otherwise.
Wall surfaces - The sides of a moulded part The message on this page is an example from view publisher site our complete White Paper 'Injection Moulding for Buyers'.
Production process for generating parts by injecting liquified product into a mould, or mold and mildew Streamlined representation of the procedure Injection moulding (U.S. spelling: injection molding) is a production process for generating components by injecting liquified product into a mould, or mold and mildew. Injection moulding can be performed with a host of products primarily including steels (for which the process is called die-casting), glasses, elastomers, confections, and also many frequently thermoplastic and also thermosetting polymers. Injection moulding is commonly utilized for producing a selection of parts, from the smallest parts to entire body panels of autos. Developments in 3D printing modern technology, using photopolymers that do not thaw during the shot moulding of some lower-temperature thermoplastics, can be used for some simple shot moulds. Shot moulding utilizes a special-purpose device that has 3 components: the injection system, the mould and the clamp.
The 2-Minute Rule for Manufacturing
, with the quantity used of the former being substantially higher.: 13 Thermoplastics are common due to features that make them extremely ideal for injection moulding, such as simplicity of recycling, versatility for a large variety of applications,: 89 and ability to soften and also flow on heating.In multiple dental caries moulds, each dental caries can be the same and also form the exact same parts or can be one-of-a-kind as well as form several various geometries throughout a single cycle. Moulds are normally made from tool steels, but stainless-steels as well as aluminium moulds are appropriate for sure applications. Aluminium moulds are usually improper for high volume production or parts with slim dimensional resistances, as they have substandard mechanical properties as well as are extra prone to put on, damage, as well as deformation throughout the injection and securing cycles; nonetheless, aluminium moulds are cost-effective in low-volume applications, as mould construction prices as well as time are substantially decreased.
The screw provides the raw product forward, mixes and homogenises the thermal and viscous distributions of the polymer, and decreases the needed heating time by mechanically shearing the material and also including a significant quantity of frictional home heating to the polymer. visit the site The material feeds forward through a check shutoff as well as gathers at the front of the screw into a volume known as a shot. When enough material has actually collected, the product is required at high pressure and also speed into the part creating dental caries. The specific quantity of contraction is a feature of the material being utilized, as well as can be reasonably foreseeable. To stop spikes in pressure, the procedure usually utilizes a transfer setting corresponding to a 9598% full cavity where the screw changes from a consistent velocity to a constant pressure control.
See This Report on Lean Production
The packing pressure is applied until the gate (dental caries entry) strengthens. Due to its small dimension, the entrance is typically the very first location to solidify through its whole thickness.: 16 Once the gateway strengthens, no more product can get in the dental caries; as necessary, the screw reciprocates and also gets product for the following cycle while the product within the mould cools down so that it can be expelled as well as be dimensionally secure.Report this wiki page